Additive Fertigung – umgangssprachlich 3D-Druck – hat wie keine andere Fertigungstechnologie in den letzten Jahren öffentliche Aufmerksamkeit erfahren und Bremen ist dabei ein Hotspot in Deutschland. Die hier ansässige Luft- und Raumfahrtindustrie ist ein wichtiger Innovationstreiber für die additive Fertigung, ebenso wie die Medizintechnik. Neben den breiten Anwendungsbereichen in der Industrie ist die additive Fertigung auch ein wichtiger Forschungsschwerpunkt in Bremen. Um dieser Entwicklung Raum zu geben und die dahinterstehende Innovationskraft Bremens sichtbar zu machen, hat der Senator für Wirtschaft, Arbeit und Häfen in Kooperation mit AIRBUS Bremen und der Materialise GmbH den Bre3D-Award ausgelobt.
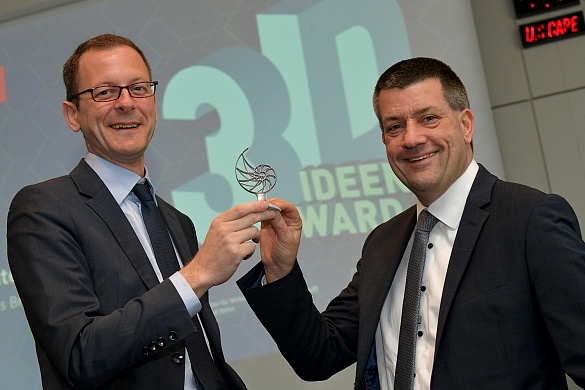
Senator Martin Günthner und André Walter (rechts), Standortleiter Airbus Bremen, mit dem Bre3D-Award
„Die Bandbreite der Einreichungen zeigten deutlich, dass die additive Fertigung längst keine Zukunftsvision, sondern ein innovativer Bestandteil der Fertigungstechnologie geworden ist. Die Technologie findet in vielen unterschiedlichen Branchen, sowohl in Großunternehmen wie auch in kleinen und mittelständischen Unternehmen ihre Anwendung. Gestützt von einem regionalen Netzwerk aus den hier ansässigen wissenschaftlichen Instituten und Forschungseinrichtungen und der Wirtschaft, haben sich Bremen und Bremerhaven dabei zu einem wichtigen deutschen Hotspot für diese Schlüsseltechnologie entwickelt. Bremens Kompetenzen in den Bereichen Material, Prozesse und Bionik stechen dabei besonders heraus,“ betont Martin Günthner, Senator für Wirtschaft, Arbeit und Häfen.
Auch André Walter, Standortleiter von Airbus in Bremen, zeigt sich begeistert: „Wir sind stolz, die Verleihung der ersten Bre3D-Awards an unserem Bremer Airbus-Standort ausrichten zu können und so der Vernetzung von Wirtschaft und Wissenschaft Raum zu geben. Die eingereichten Projekte zeigen, wie vielfältig nutzbar der 3D-Druck in den verschiedensten Branchen ist. Da kann jeder noch etwas vom anderen lernen!“
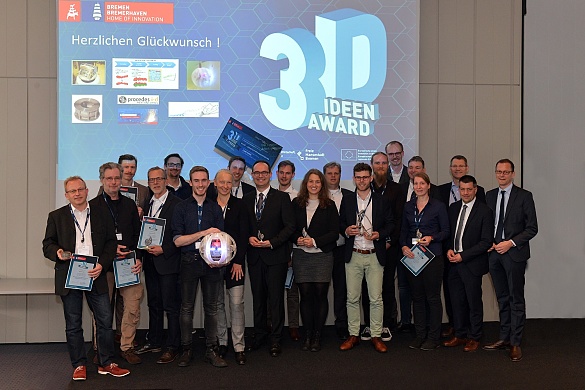
Die Gewinnerteams mit André Walter (2. v.r.) und Senator Günthner (rechts)
"Die Initiative Bre3D-Award des Senators für Wirtschaft, Arbeit und Häfen der Freien Hansestadt Bremen sehen wir als wichtigen Impuls, um den Einsatz additiver Fertigung in der Region zu fördern und so die Wettbewerbsfähigkeit regionaler Unternehmen zu steigern. Als ein führender Anbieter von Dienstleistungen und Softwarelösungen rund um den 3D-Druck mit Standort in Bremen freuen wir uns daher sehr, uns als Jurymitglied und Kooperationspartner einbringen zu dürfen. Wir unterstützen die Gewinner gerne mit unseren 3D-Druck Produktionskapazitäten bei der Umsetzung ihrer Projekte. Zusätzlich wird der Erfolg der eingereichten Projekte mit den von uns gedruckten Pokalen aus Metall und Kunststoff entsprechend gewürdigt und sichtbar gemacht," so Marcus Joppe, Managing Director Materialise Deutschland.
Unter dem Motto „Zeigt her, was ihr könnt!“ wurden innovative Ideen in insgesamt sieben Kategorien vergeben.
Folgende Projekte sind jeweils mit dem ersten Preis ausgezeichnet worden.
Kategorie Materialien und Werkstoffe:
- MAPS (Material Processing/Printing for Aerospace)
Die Innovation der Einreichung MAPS liegt im Bruch des Dogmas "Material nicht schweißbar = nicht druckbar" und in einem stark vereinfachten Design. Dies stellt eine signifikante Erweiterung der Materialbasis dar.
TEAM
Detlev Konigorski (Airbus) und Torsten Vogel (Airbus Defence and Space)
Kategorie Prozesse und Verfahren:
- Kaustik
Das Ziel des Forschungsprojektes lag in einer vollständig automatisierten Datenaufbereitung im Rahmen der Serienfertigung von dentalen Bauteilen durch einen Laserstrahlschmelzprozess (LBM). Der im Projekt entwickelte Softwareprototyp ist in der Lage eine automatisierte Datenaufbereitung umzusetzen. Dabei werden Datensätze, die von der Qualitätskontrolle freigegeben werden, direkt und vollautomatisch vorbereitet und auf der vorgesehenen Bauplattform platziert.
TEAM
Christian Kober (ISEMP) und Sabrina Bergel (BEGO Medical)
Kategorie Bionik und Design:
- SAUV – Die Klügere gibt nach
Konventionelle Unterwasserdrohnen gefährden durch ihre feste Gehäusestruktur die Sicherheit von Tauchern, Material und Umwelt. Bislang wurde versucht, diese Risiken durch komplexe Steuerungssysteme zu minimieren. Das innovative SAUV-System (Soft Robotic Autonomous Underwater Vehicle) besitzt ein von biologischen Einzellern inspiriertes flexibles Exoskelett. Dessen Einzelkomponenten wurden mittels speziell entwickelten additiven Fertigungstechniken (FDM) aus verschiedenen Polymerarten gedruckt. Die innovative Bauform und intelligente Steuerung mittels neuronaler Netze ermöglichen den gefahrlosen Einsatz des SAUV-Systems in direkter Nähe zu Tauchern und empfindlichen Umgebungen.
TEAM
Hochschule Bremen: Prof. Dr. Jan-Henning Dirks, Prof. Dr. Susanna Labisch und Fabian Plum
Kategorie Funktionsintegration:
- RK 16-AM: Rückschlagventil mit stark verbesserten Eigenschaften
Ziel war es, eine bestehende Armatur hinsichtlich Gewicht, Fertigungsaufwand, Funktion und Strömungsverhalten zu optimieren. Als Forschungsobjekt wurde ein Rückschlagventil gewählt. Es wird meist aus einem teuren Werkstoff (Titan) mit erheblichem Fertigungsaufwand und hohem Werkzeugverschleiß hergestellt und weist dabei lediglich ein nur durchschnittliches Strömungsverhalten auf. Im Ergebnis konnte mittels der additiven Fertigung ein optimiertes Armaturengehäuse konzipiert werden, welches die einzelnen Anforderungen optimal in sich vereint.
TEAM
Manon Vietz (GESTRA), Wolfgang Hansen (GESTRA), Michael Kopa (GESTRA) und Stephan Winters (GESTRA)
Kategorie Produkte und wirtschaftliche Anwendung:
- Messebau: 3D-Druckelemente als Verbinder, Endkappen
von Aluminiumprofilen
Um die starren Aluminiumprofile, welche beim Messebau zum Einsatz kommen, in vielseitige, komplexe Konstrukte zu wandeln, wurden für das Projekt 3D-Druckecken als Verbindungsstücke getestet. Darüber hinaus wurden Profilendkappen, Schutzkappen, Adapter und nicht zuletzt zur Bemusterung neuer Profile oder anderer Bauteile additiv gefertigt.
Diese Bauteile werden in herkömmlichen Verfahren aufwendig konstruiert und aus verschieden Werkstoffen gefräst oder von Hand gefertigt. Dieses Produktionsverfahren ist zeitintensiv, teuer und anfällig für Fehler. Mittels des im Projekt entwickelten FDM-Verfahren können der Zeitaufwand sowie die Kosten stark reduziert werden.
TEAM
Gabriel Barth (procedes i-d)
Kategorie Startups:
- ELISE – Generative Engineering
Die additive Fertigung erlaubt wirtschaftliche Bauweisen insbesondere dann, wenn die neuen Gestaltungsfreiheiten gewinnbringend eingesetzt werden. Die ELISE GmbH will Produktentstehungsprozesse mit einer eigens dafür entwickelten Software digitalisieren, um so zum ersten Mal bionische Konstruktionsprinzipien in der Bauteilentwicklung zu ermöglichen.
Damit sind Anwenderinnen und Anwender in der Lage, komplexe Bauteile unter Berücksichtigung unterschiedlicher Randbedingungen mittels Algorithmen automatisiert zu entwickeln.
TEAM
ELISE GmbH: Sebastian Möller, Dr. Moritz Maier, Daniel Siegel und Robert Naguschewski
Sonderpreis Ausbildung und Training:
- 3D-Druck als Ausbildungsbestandteil für alle Auszubildenden der DB Fahrzeuginstandhaltung GmbH
Die DB Fahrzeuginstandhaltung GmbH will durch dezidierte Ansprache und Schulung ihrer Auszubildenden für die Möglichkeiten der additiven Fertigung sensibilisieren. Durch die Implementierung dieses innovativen Prozesses als Teil der regulären Ausbildung soll gewährleistet werden, dass die Technologie des 3D-Druck fester Bestandteil des Know-Hows zukünftiger Fachkräfte wird.
TEAM
Falk Pohl (DB BRE) und Johannes Hofmann (DB BRE )
Im Download:
Booklet "Einreichungen für den Bre3D-Award" PDF-Datei (pdf, 4.3 MB)
Fotos: Senator für Wirtschaft, Arbeit und Häfen
Ansprechpartner für die Medien:
Tim Cordßen
Pressesprecher beim Senator für Wirtschaft, Arbeit und Häfen
Tel.: (0421) 361-8746
E-Mail: tim.cordssen@wah.bremen.de